
Were carefully redried at 120 C under vacuum for at least 8 h. Immediately quenched in a water bath, and finally pelletized. Least 8 h, then blended by using a twin-screw extruder (Automatic ZCM 32/36) at 285 C and at fixed rotor speed at 240 rpm, Materials were carefully dried at 120 C under vacuum for at The reinforced polymer of LCP was Vectra A950 manufactured by Hoechst
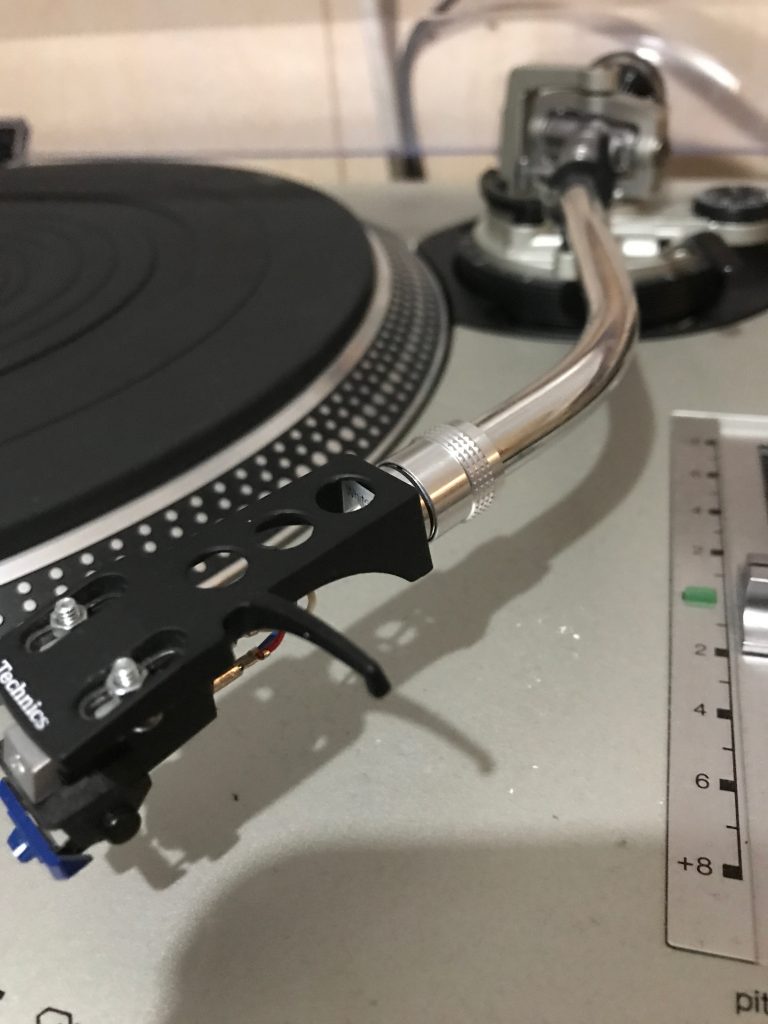
Phenol/o-dichlorobenzene at 25 C) manufactured by Kolon Ltd, (I.V = 0.51: inherent viscosity of a solution in The matrix polymer of poly(ethylene 2.6-naphthalate) (PEN) was KP 785 Observed mechanical properties were correlated to the morphology Mechanical and morphological characteristics of these blends and the Was manufactured on a pilot scale by Kolon Ltd. A matrix polymer of poly(ethylene 2,6-naphthalate) (PEN) But PEN is a matrix polymer that has not been
Lcps synergy Pc#
PBT, PET, and PC are matrix polymers that have been Molded blends of a polyester-type thermotropic LCP with poly(ethyleneĢ.6-naphthalate). In this paper we focus on twin-screw extruder blended and injection The blends have been processed byĮxtrusion, melt spinning, injection molding, and compression molding. Commercial or experimental LCPs haveīeen blended with many thermoplastics, e.g., poly(butylene terephthalate) (PBT) (3, 5), poly(ethylene terephthalate) (PET) (6-10),Īnd polycarbonate (PC) (5, 1115). Several researchers have studied blends of thermotropic LCPs and Process because of its relatively low melt viscosity. Of a thermotropic LCP can also make some thermoplastics easier to Matrix polymer or to improve its dimensional stability. LCPs are blended with thermoplastics mainly to reinforce the Good properties of LCPs can be transferred into a more flexible matrix By blending thermotropic main-chain LCPs withĮngineering thermoplastics, the highly ordered fibrous structure and Processing combined with high performance characteristics makes theīlend composed of thermotropic LCP and engineering plastics veryĪttractive (3, 4). The mechanical properties are also of interest (3). The blends of LCPs with other engineering plastics to enhance Of their potential application as ultra-high strength fibers and moldedĪrticles. Thermotropic liquid crystalline polymers (TLCPs) are attractive because There has been aĬonsiderable interest in liquid crystalline polymers (LCPs), especiallyĪfter the development of high modulus and high strength fibers preparedįrom the lyotropic aromatic polyamides (aramids) by DuPont (1, 2). Meet desired stiffness and strength requirements. Which may be tailored by controlling constituents and microstructure to
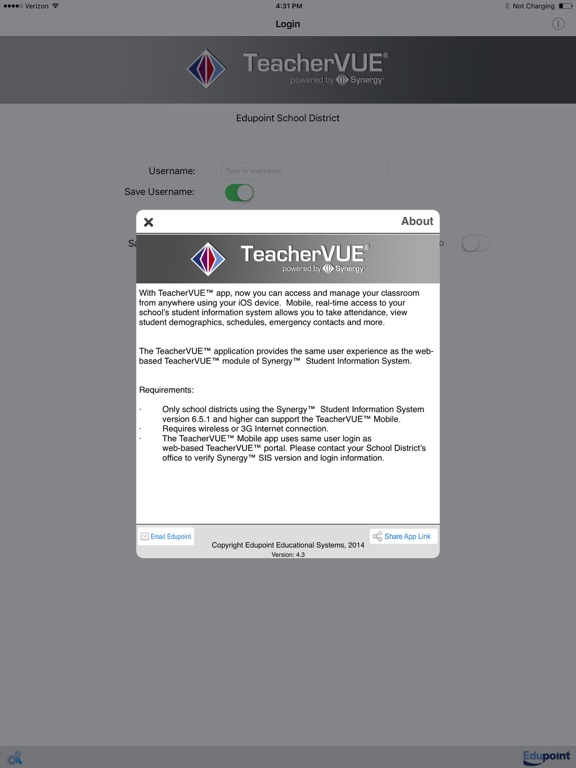
These materials are unique engineering materials, Properties, performance, costs, and the potential of the availableĬomposite material. As technologyĪdvances, it becomes increasingly important to understand the

Synergistically to solve the needs of the application.
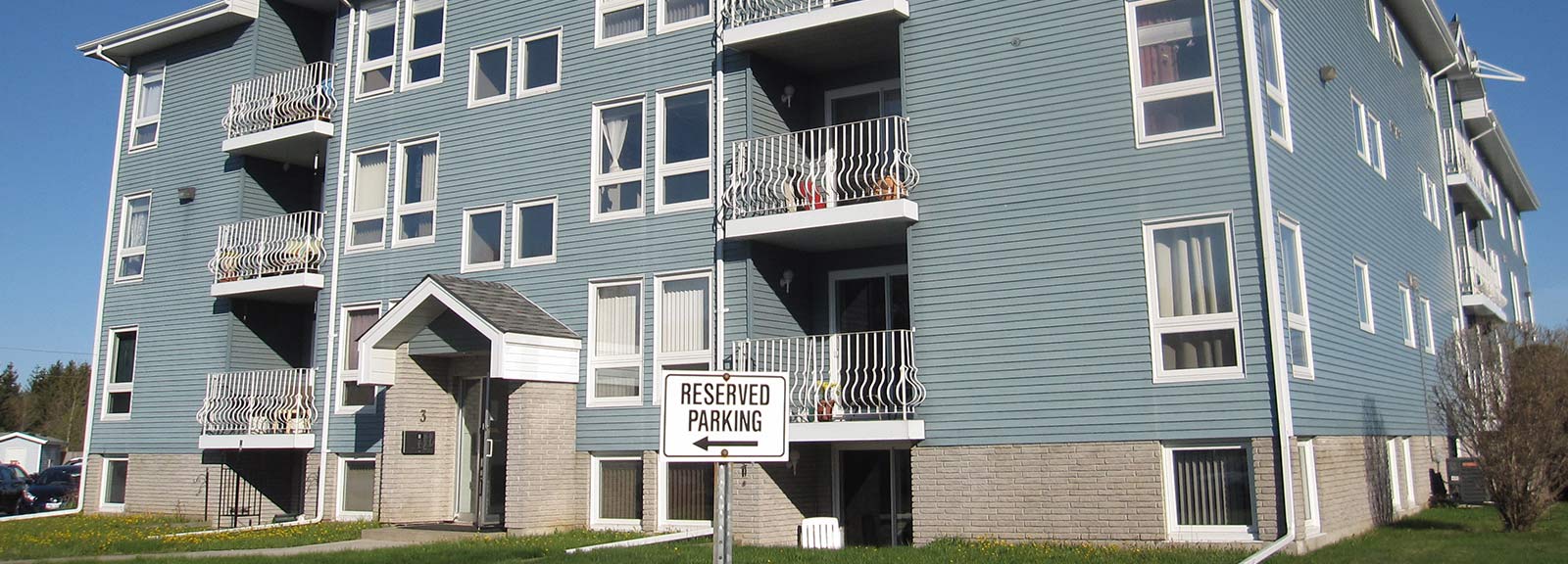
Satisfied by utilizing a composite material whose constituents act These requirements, which often involve aĬombination of many difficult-to-attain properties, can often be Materials that satisfy more stringent requirements, such as high tensile Growing industrial activities create a continual demand for improved
Lcps synergy free#
